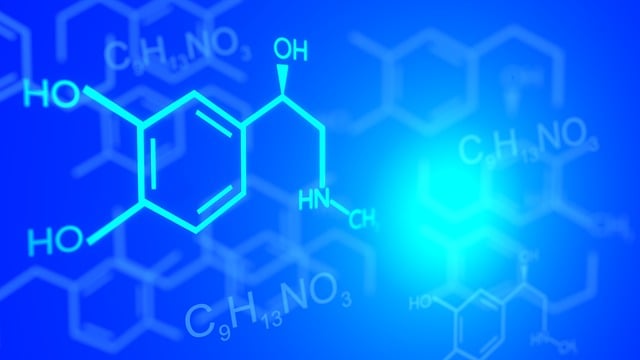
How chemical manufacturing ERP solves industry challenges
Chemical Manufacturing ERP – the solution that combines proven technology with a flexible structure. As an industry, chemical manufacturing faces unique challenges. You need to make important decisions fast with so much on the line. Though each chemical manufacturing business has different needs, most have similar software challenges. Here’s how a chemical manufacturing ERP solution […]
Diane Harvey