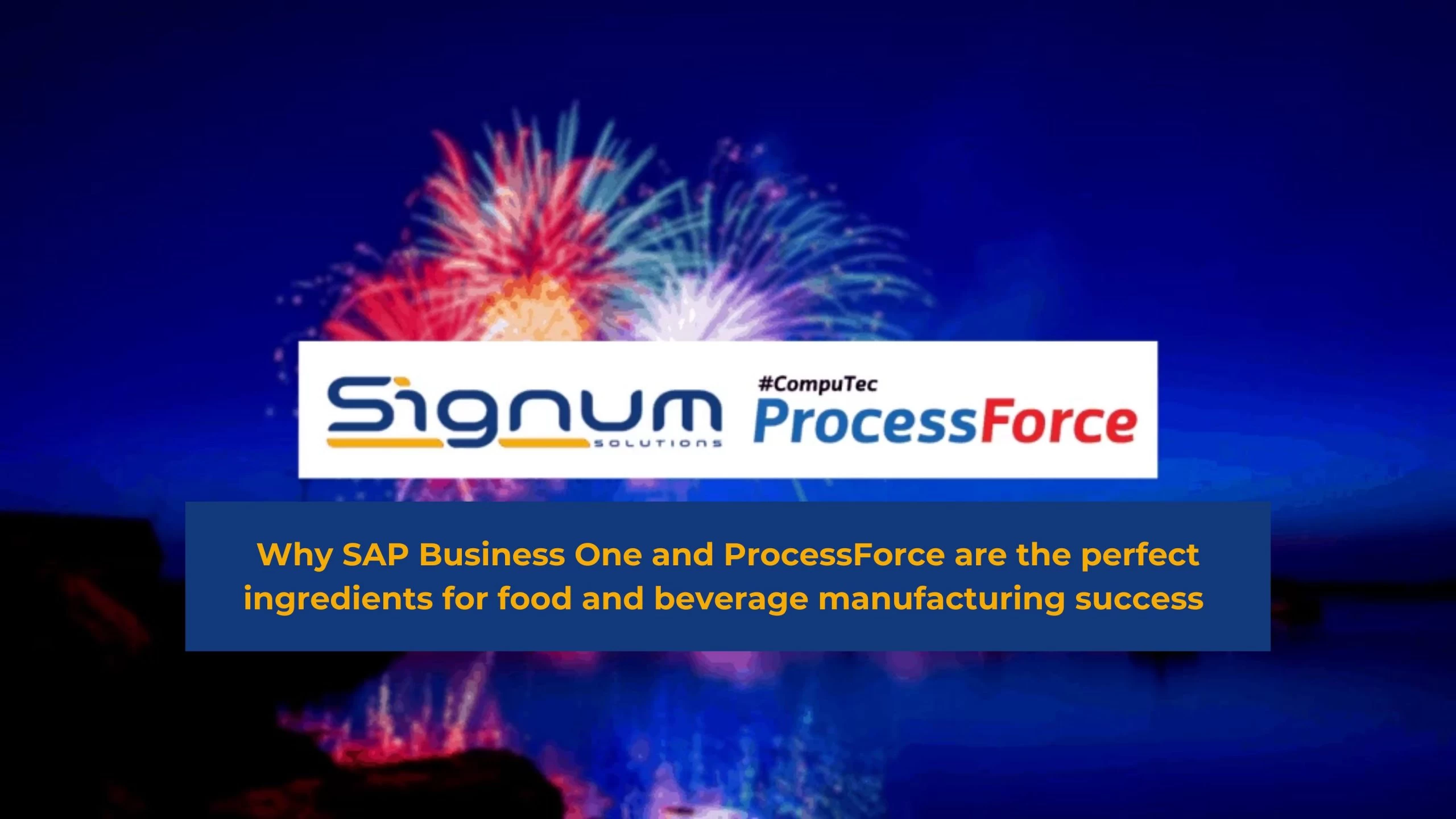
Why SAP Business One and ProcessForce are the perfect ingredients for food and beverage manufacturing success
In this article, we are going to take a look at Why SAP Business One and ProcessForce are the perfect ingredients for food and beverage manufacturing success. Food and beverage manufacturing is a complex and challenging industry that requires constant innovation, adaptation, and compliance. Whether you are producing snacks, drinks, dairy products, or any other […]
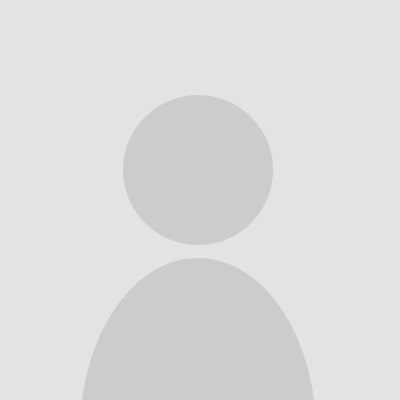
Diane Harvey