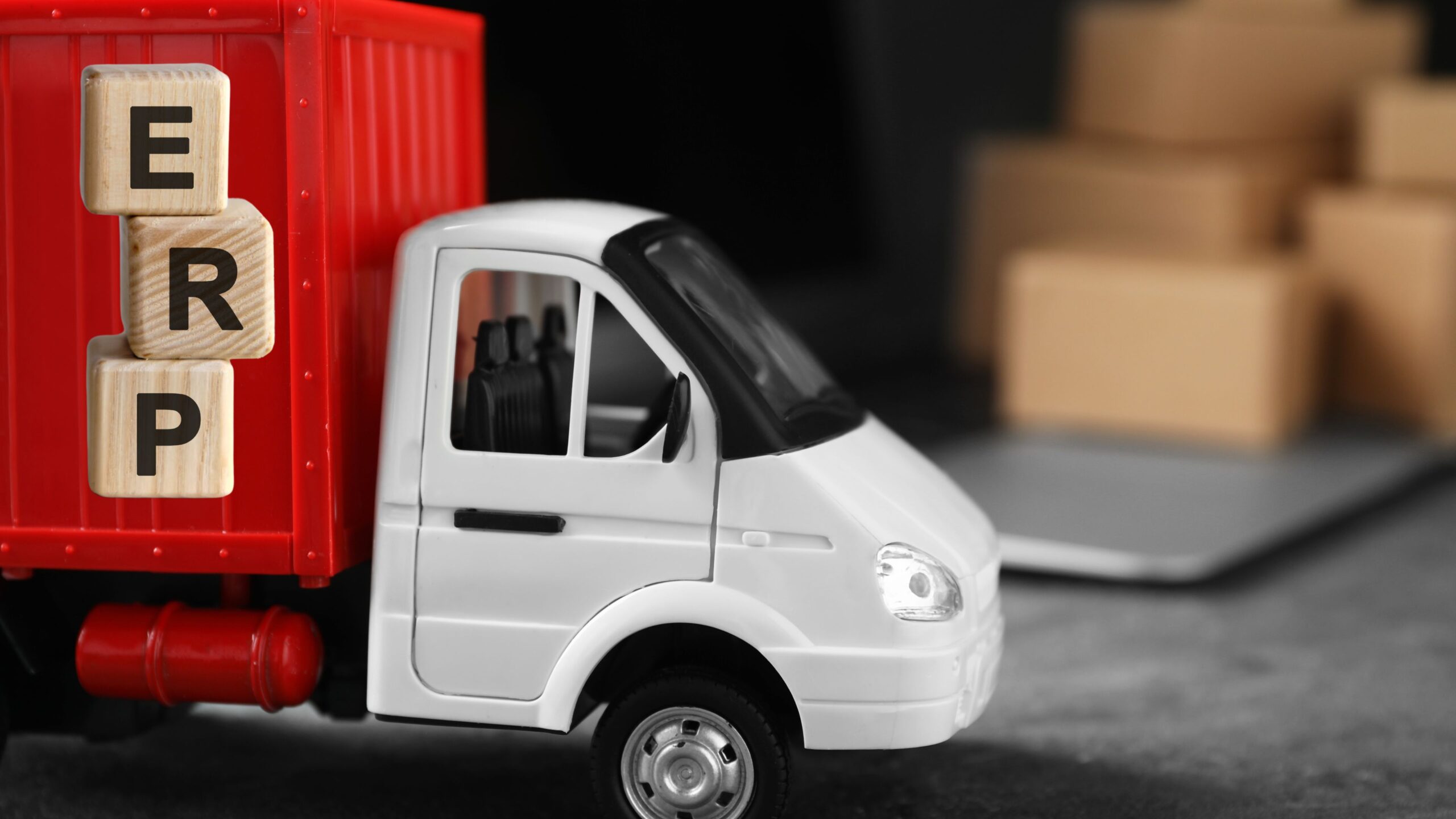
Streamlining Operations with ERP for Wholesale Distribution
Wholesale distribution is a demanding industry that requires managing multiple aspects of the supply chain efficiently. From inventory management to order fulfilment, wholesale distributors face unique challenges that demand robust solutions. This is where ERP for wholesale distribution comes in—a powerful tool to streamline operations, reduce costs, and improve customer satisfaction. What is ERP for […]
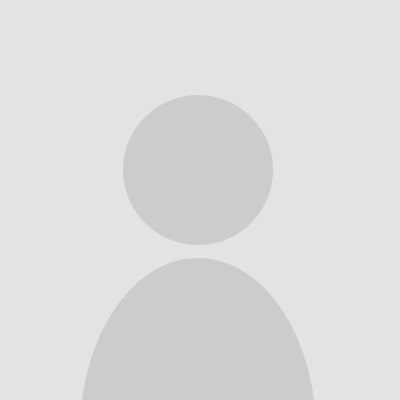
Diane Harvey