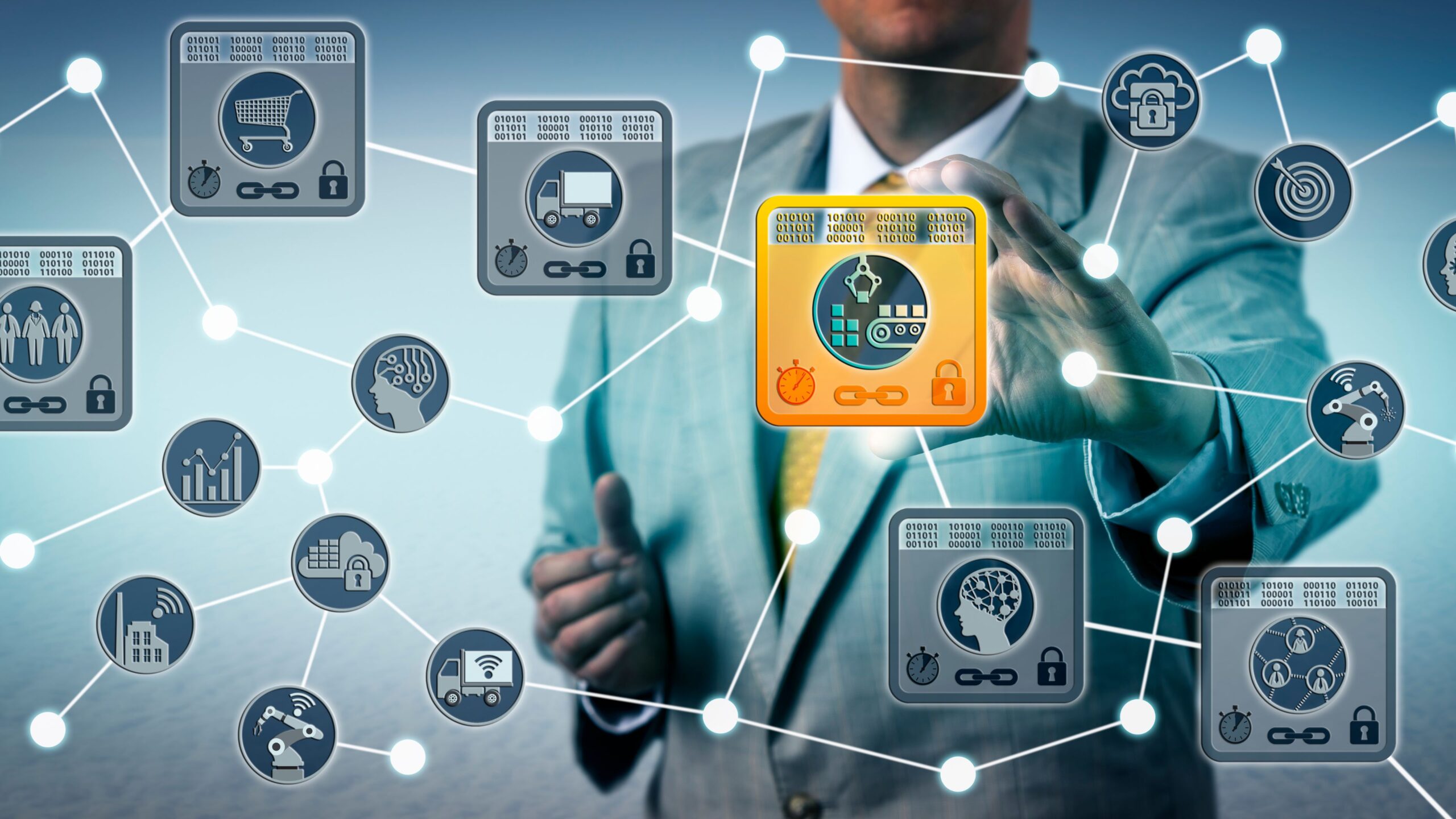
How Can ERP Solutions Enhance Batch Traceability in the Food Industry?
In today’s highly regulated and consumer-conscious food industry, maintaining rigorous batch traceability has become a cornerstone of operational integrity. Batch traceability in the food industry not only ensures compliance with global safety standards but also fortifies consumer trust and safeguards public health. Enterprise Resource Planning (ERP) systems, especially those tailored for the food industry like […]
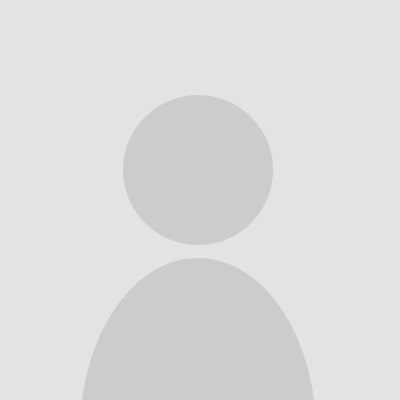
Diane Harvey