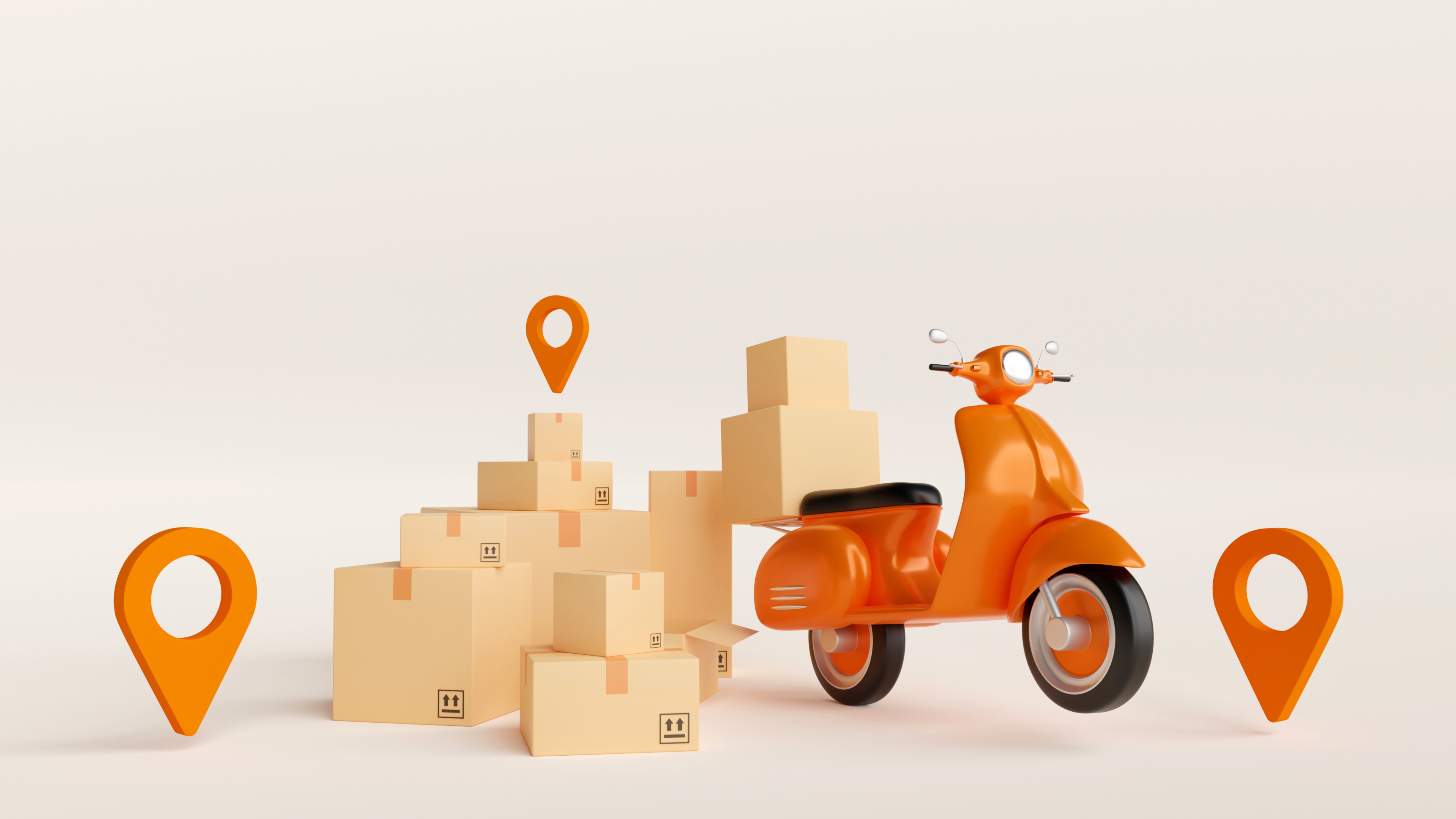
Optimising Operations with Foodservice ERP: A Guide for Food Wholesalers and Distributors
In the competitive landscape of the foodservice industry, leveraging a foodservice ERP solution is crucial for businesses aiming to enhance operational efficiency and profitability. These business systems are designed with the unique needs of food wholesalers and distributors in mind, streamlining processes from the ground up. Real-Time Insights and Efficiency through Foodservice ERP A cornerstone […]
Diane Harvey